BOLT_FAILURE
Contact and tied interfaces
"Optional title"
coid
pid, tid, $T_{fail}$, $S_{fail}$, $W_{fail}$
Parameter definition
Description
This command is used to define criteria for bolt failure. Bolts are identified through a list of coordinates in a TABLE. The coordinates are points on the surface of, or inside, the bolts. IMPETUS Solver will automatically identify the bolt elements and keep track of resultant forces and absorbed energies. Forces and energy levels are written to bolt_force.out.
A damage parameter $D$ is defined as:
$\displaystyle{ D = \mathrm{min} \left[ \sqrt{ \left( \frac{\mathrm{max}(0, T)}{T_{fail}}\right)^2 + \left( \frac{S}{S_{fail}} \right)^2 }, \frac{W}{W_{fail}} \right] }$
where $T$ and $S$ are the total tensile and shear forces in the bolt and $W$ is the absorbed energy (including elastic work). All bolt elements are eroded when damage reaches $D=1$. If no failure parameters are defined damage will not be computed. The command can then still be used to track and output force and energy levels.
An accurate calculation of the shear forces requires a relatively fine mesh. The shear zone (which can be extremely narrow) does not need to be resolved. However, as a rule of thumb, the element size in the axial direction of the bolt should not be larger than the thickness of the individual plates.
Example
Table with two bolts
A simple example showing how to list bolt coordinates in a TABLE.
Pressure loaded plate
In this example (complete input below) a bolted circular plate is exposed to a constant pressure load. The model runs in two steps. In Step 1 the bolts are pre-loaded using PRESTRESS_BOLT. The pressure is applied in Step 2.
A TABLE (ID=100) is used to define the location of the bolt holes (TRIM_HOLE). The same table is used by the commands COMPONENT_BOLT and BOLT_FAILURE. Note that BOLT_FAILURE only uses the first four columns of data in the table (bolt ID and location).
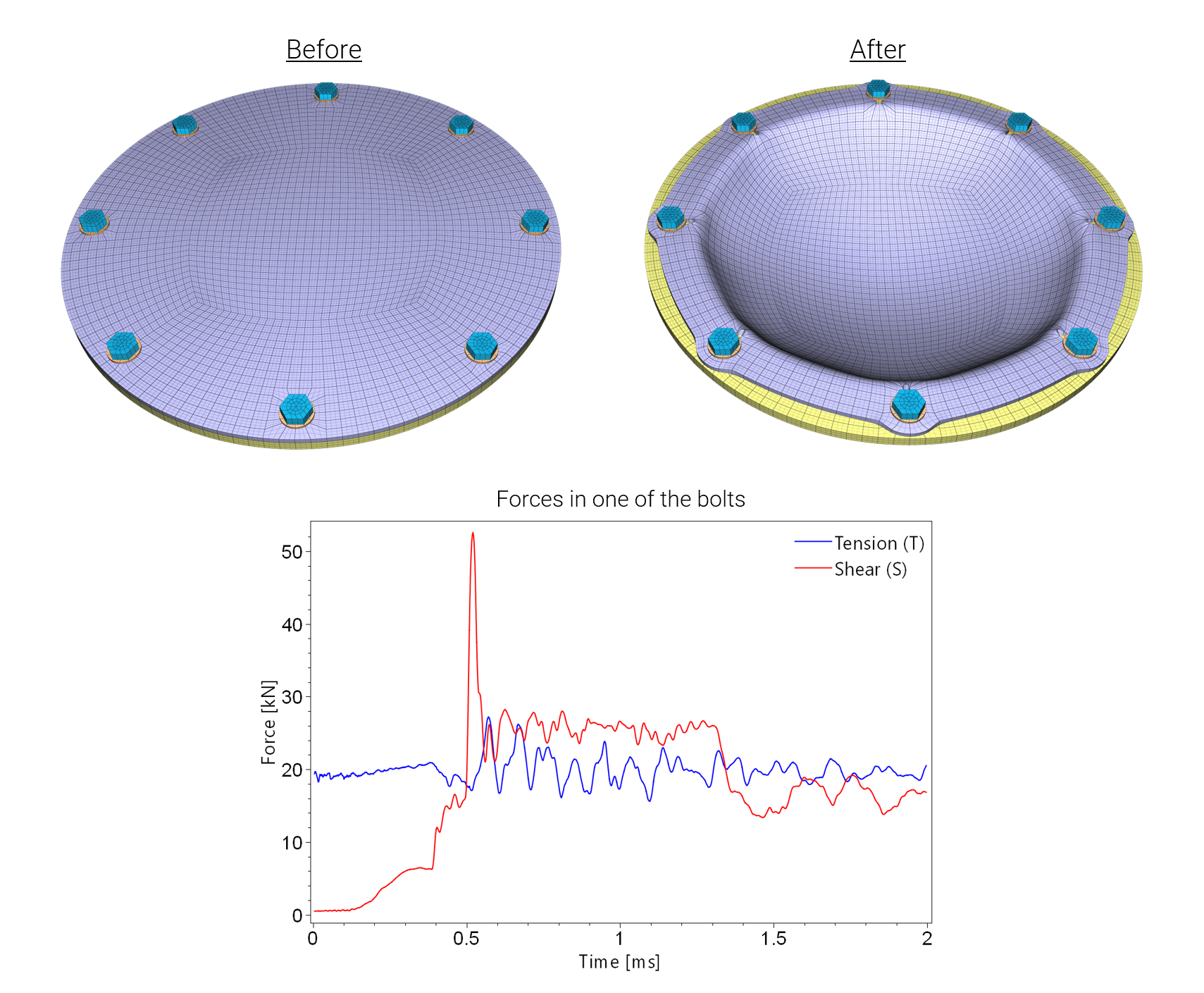
common.k (commands and parameters used in both steps):
step_1/main_step_1.k (prestress bolts):
step_2/main_step_2.k (pressure load on plate):