CONNECTOR_DAMPER
Mesh commands
"Optional title"
coid
pid${}_1$, pid${}_2$, csysid, $R$, $h$, $m$, $\eta$, $k_{max}$
cid${}_{axial}$, cid${}_{shear}$, cid${}_{bend}$, cid${}_{rate}$
Parameter definition
Description
This command is used to model the effect of a rubber damper between two parts (pid${}_1$ and pid${}_2$). The nodes enclosed inside the cylinder defined by csysid, $R$ and $h$ are used to calculate the damper deformations. The computed forces are distributed to the same set of nodes.
The hysteresis parameter $\eta$ is a scalar between 0 and 1. It tells by how much the forces are reduced during unloading. $\eta=0.2$ means that the unloading force is 20% lower than during loading.
$k_{max}$ limits the tangential stiffness. It is primarily used to prevent discrete jumps in force when oscillating between loading and unloading.
Example
Axially loaded damper (quasi-static and at velocity 1m/s)
As complete model whith a damper between two plates. It is first compressed and then loaded in tension.
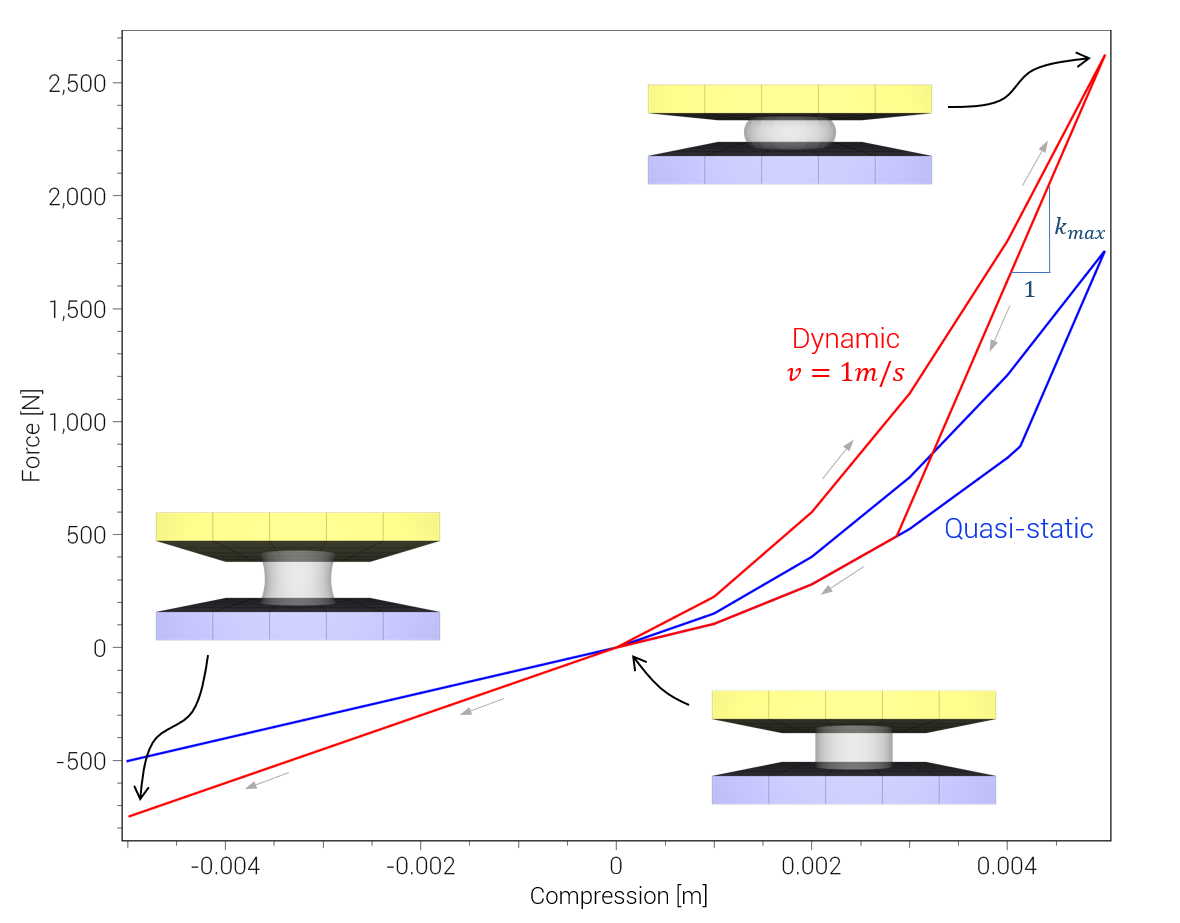