MAT_MMC_OST
Material properties
Beta command
This command is in the beta stage and the format may change over time.
"Optional title"
mid, $\rho_0$, $G$
$\sigma_c$, $\sigma_x$, $p_x$, $\sigma_{cap}$, $c_{1,f}$, $\sigma_{cap,f}$, $\varepsilon_{p,f}$, $s$
$K_1$, $K_2$, $K_3$, $yield$, $\beta$, $\varepsilon_{v,max}$, $c$, $\dot{\varepsilon}_0$
$\psi$, $d$, $d_{dec}$, nsplit
Parameter definition
Description
This is a ceramic model (by Marcus Menchawi and Thomas Öst) with a pressure dependent shear resistance. The pressure dependency of undamaged material is defined from two points on the yield strength vs. pressure curve and a yield strength cap.
Pressure
The pressure-volume relationship is cubic in compression:
$p = K_1 \mu + K_2 \mu^2 + K_3 \mu^3 \;\;\; \mu > 0$
and linear in tension:
$p = K_1 \mu \;\;\; \mu \lt 0$
where:
$\mu = \rho/\rho_0 - 1$
Yield strength
The yield strength vs. pressure curve is defined as a combination of two functions. $C^1$ continuity prevails in the transition between the two functions and the transition is defined at a pressure $p_t$, defined as:
$\displaystyle{p_t = max\left(\frac{\sigma_c}{3}, p_x\right)}$
The yield strength, $\sigma_y$ vs. pressure, $p$, is defined as:
$\sigma_y(p) = \left\{ \begin{array}{cc} \displaystyle{c_1 \cdot p + c_2} &: p \leq p_t\\ \displaystyle{\sigma_{cap} \cdot \left(1.0 - exp\left(-c_3 \cdot p + c_4\right)\right)} &: p \gt p_t \end{array} \right. $
Parameters $c_1$ to $c_4$ are calculated and set in the solver based on given input.
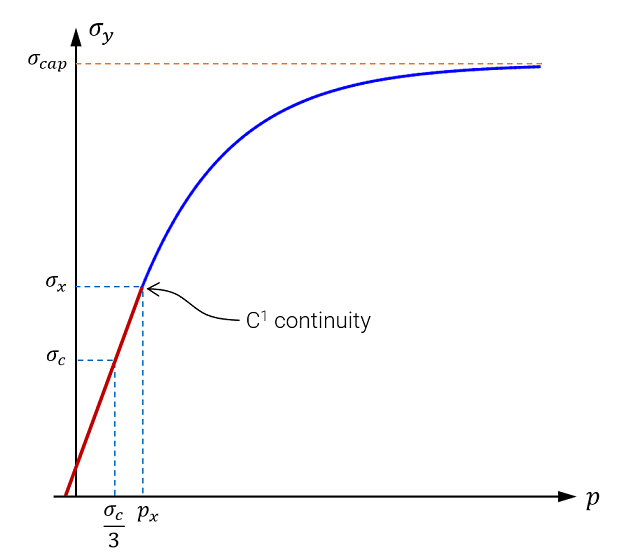
By default, von Mises yield surface is used (yield = 0.0). A Rankine surface is defined by setting yield = 1.0. Values between 0.0 and 1.0 are accepted to achieve a combination of the two surfaces.
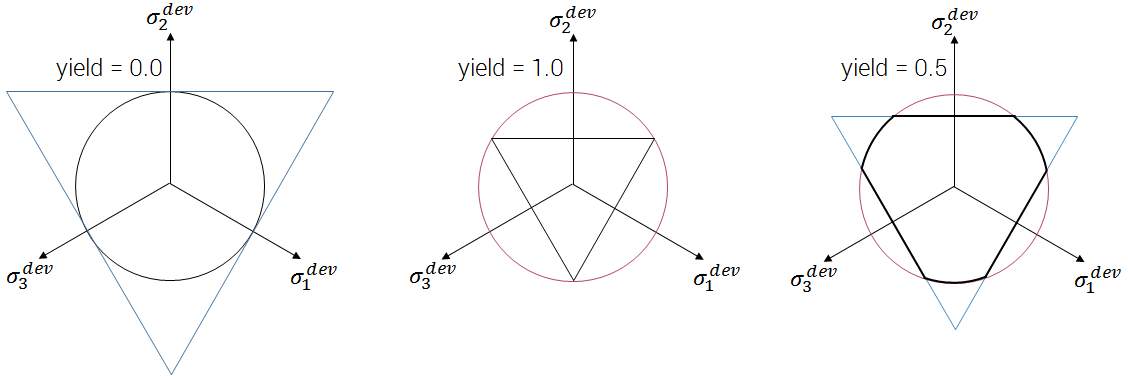
Plastic flow is optional and included by setting $\varepsilon_{p,f} \gt 0$ or by providing a CURVE defining failure strain as function of pressure. With zero as input, the material becomes linear-elastic up to failure and the material strength vs. pressure curve coincides with the yield strength vs. pressure curve. Dilatation is optional during plastic flow and limited by $\varepsilon_{v,max}$. Dilatation is included by defining $\beta$ and $\varepsilon_{v,max} \gt 0.0$. Associated plastic flow is achieved with $\beta = 1.0$.
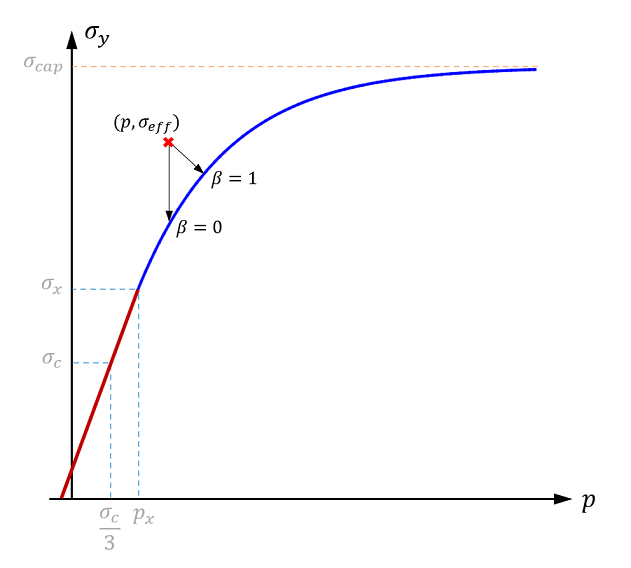
The shear resistance (flow stress) of failed material is defined from parameters $c_{1,f}$ and $\sigma_{cap,f}$.
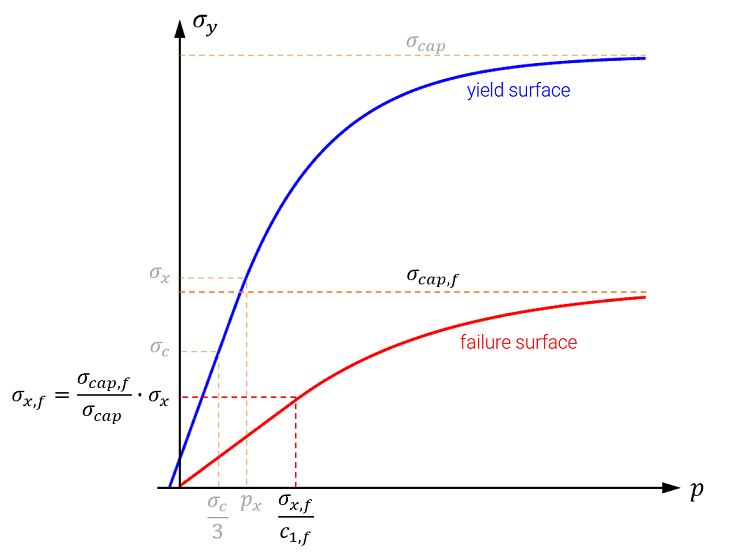
Rate effects
Strain rate effects are included by increasing the quasi-static yield strength by a factor $rfac$, calculated as:
$\displaystyle{rfac = \left(1.0 + \frac{\dot{\varepsilon}^{eff}}{\varepsilon_0}\right)^c}$
With $\psi = 0.0$ (default), the hydrostatic tensile strength is not affected by the strain rate effects. $\psi = 1.0$ means that the hydrostatic tensile strength also is scaled by the factor $rfac$.
Damage
Damage, $D$, is a function of the effective plastic strain, $\varepsilon^{eff}_p$, and develops gradually from 0 to 1:
$\displaystyle{D = min \left(1.0, \frac{\varepsilon^{eff}_p}{\varepsilon_{p,f}}\right)}$
$\varepsilon_{p,f}$ is either a constant or a user defined function of pressure.
With parameter $s > 0$ , the hydrostatic tensile strength is gradually reduced with damage $D$ by applying a damage softening factor, $sfac$:
$\displaystyle{sfac = 1 - D^s}$
With $s = 0$, the hydrostatic tensile strength is instantaneously reduced from the value of intact material to zero once $D = 1$.